Plastisol ink is a paste that combines PVC resins, plasticizers, fillers, and pigments that make up the ink that many garments are printed with.
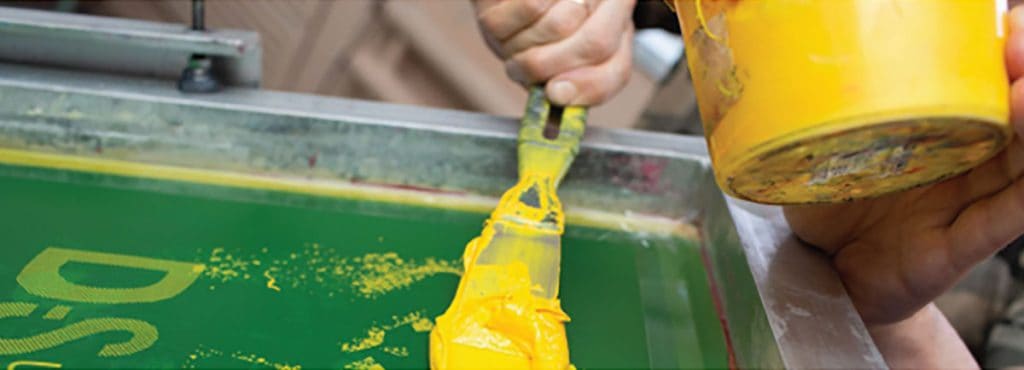
Plastisol by nature is heavier and thicker than other inks such as waterbased or other solvent inks. The structured nature of the ink is thixotropic. This means that when shaken, agitated, shear-stressed, or otherwise stressed the ink will thin out. This is most visible in colder climates where the ink has thickened and needs premixing prior to going on press.
White plastisol is the critical foundation of all PVC plastisol, it is effectively the root of a tree. White plastisol has the highest specific density by weight, and provides the opacity required when printing directly over dark garments.
Curing Plastisol Prints
For plastisol to cure, the entire ink layer needs to hit a fusion (cure) temperature of 149°( (unless using a low cure plastisol).
This is usually completed with a tunnel dryer (oven), or by flash curing and finishing with a heat press. Plastisol will not air dry.
Insufficient curing will show via wash fastness issues, cracking, fading, peeling, etc.
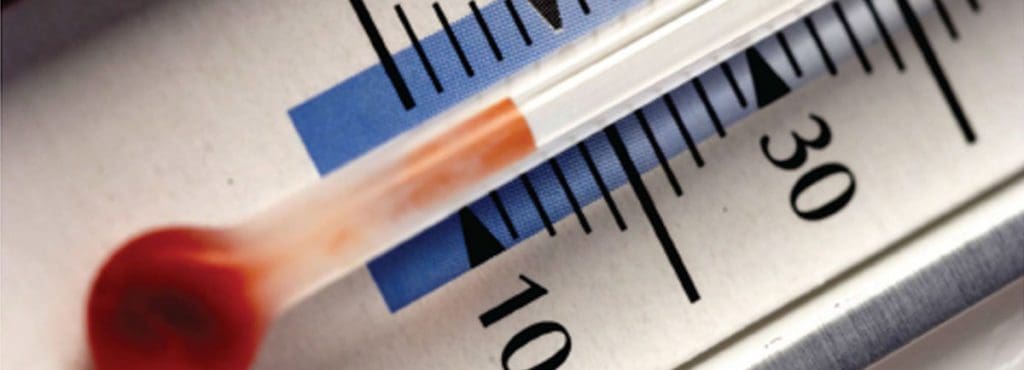
What type of squeegee is good for printing plastisol?
Traditionally, the best squeegee to use for manual printing is a 75-shore medium hardness. The great thing about using a 75-shore squeegee is that it allows for producing intricate detail, while allowing great ink penetration into the fabric you are printing on.
On auto and semi auto machines, a triple durometer rubber 75 shore/95 shore/75 shore may be used. The hard core provides good print pressure, while the 75 shore outers still provide some flex to give good ink lay down.
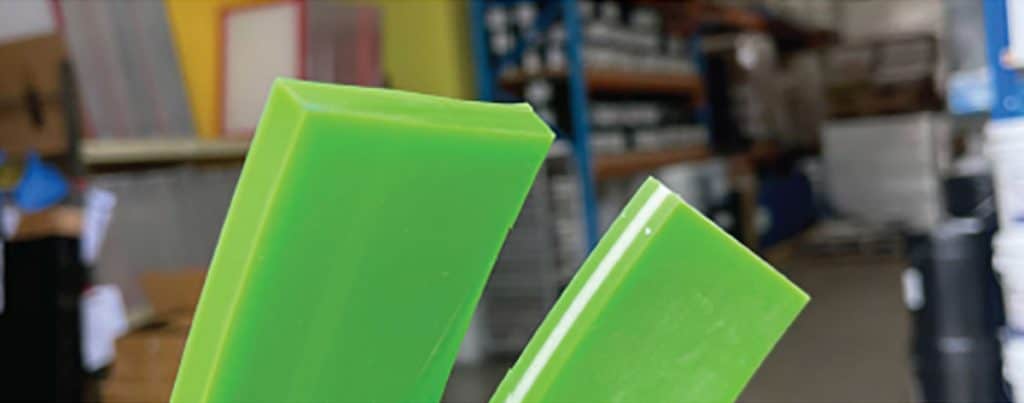
Benefits of working with plastisol?
- Cost effective – plastisol ink is relatively cheap and allows for long production runs at high speeds. Some shops have been known to achieve up to 700 units per hour.
- Plastisol, when used correctly, can be used over a range of substrates.
- Plastisol is non-drying in the screen. You won’t be dealing with your ink drying up in the screen – a peace of mind when you go for lunch and come back to finish up the job!
- There are generally plenty of different bases and additives available to print onto just about any fabric type.
- A large variety of special effect inks are available, as well as mixing systems that allow you to mix to customer colour specifications.
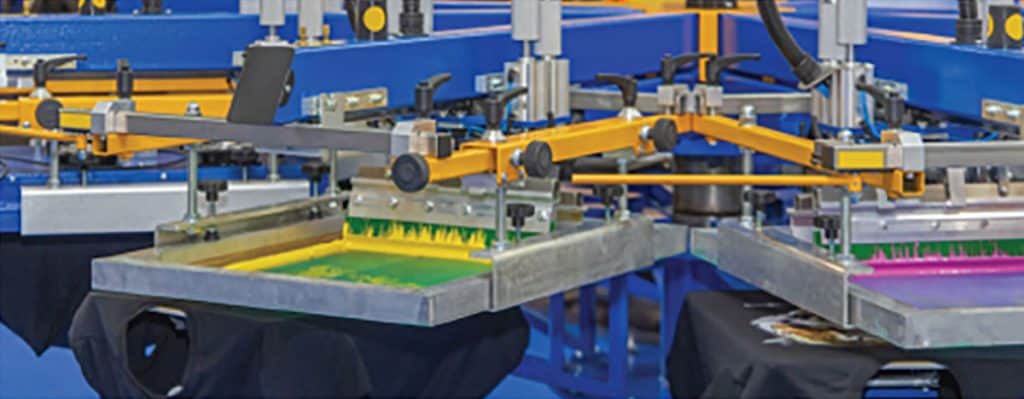
Quick tips Working with plastisol
- Make sure you have good screen tension; this helps you push the ink through the mesh and allows the mesh to re-bound quickly.
- When running plastisol on an automatic press, make sure to keep all screens well hydrated with ink to avoid production down time.
- Always give the ink a thorough mix before use. This will ensure that the ink is consistent and easier to handle on press, reducing after flash tack.
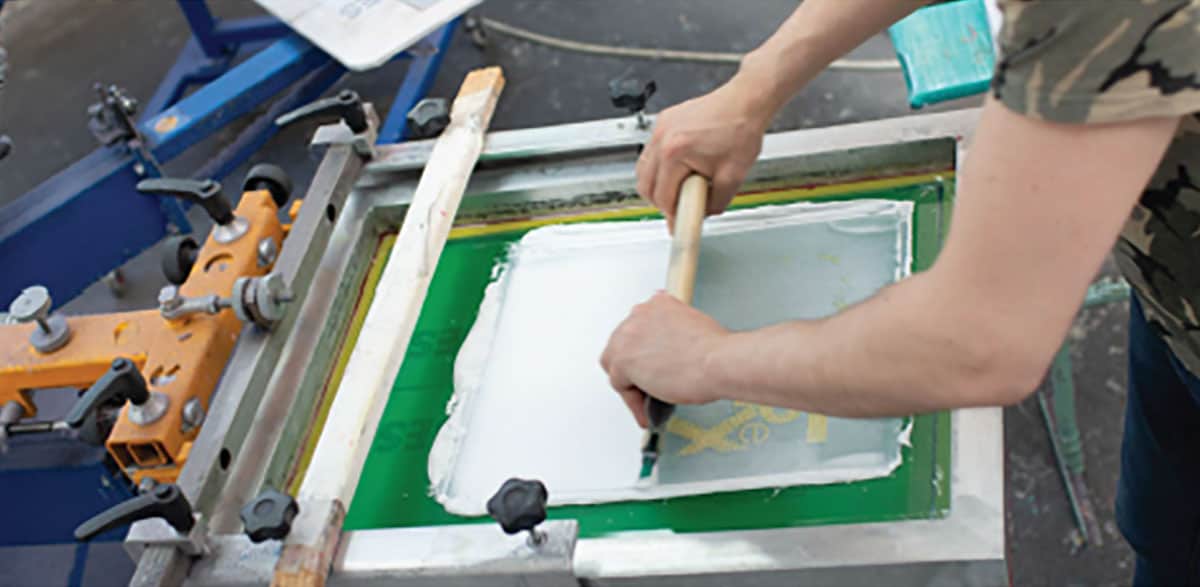
Recommended plastisol whites to work with Cotton:
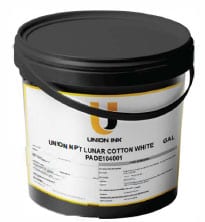
Cotton
To achieve a smooth print, you should try to use a specific cotton white that has no blowing agents that may puff the ink up. We recommend using Union Lunar Cotton White or Rutland SF2 Cotton White.
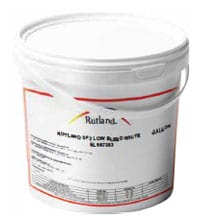
Cotton/poly blend (80/20):
With blends, it is recommended that you use a low bleed ink with excellent bleed properties. The ink should be well mixed prior to printing. To achieve
great results, we recommend using Union Diamond White, Rutland Street Fighter 2 Low Bleed White and Rutland Low Bleed Premier White.
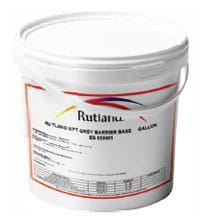
Polyester/Nylon/Athletic Wear:
Before commencing production, it Is highly recommended to perform a pre-test on the substrate you are intending to print on. This is due to dye migration that can occur with polyester fabrics. If dye migration occurs, we recommend using a blocking grey underbase or a high-level low bleed white. We recommend printing with Rutland Low Bleed Super Poly White, or the Rutland Blocking Grey Base for the best finished results.
What is Plastisol Ink? For Beginners
Our Recommendations
Setup:
High quality stencil – For t hose in high production, we recommend using Chromaline CP Tex or Murakami T9 pure polymer emulsions for high quality stencil creation. These emulsions are designed to
withstand long and high-volume run s.
On Press:
For those w ho are manual printing, mix your ink prior to printing. You can use a drill mix attachment, a cake mixer, whatever you have at hand. For larger volume printers working on an automatic press, it is
recommended to run your ink through a turnabout mixer to allow the ink to warm up, this w ill improve on press performance.
Washup:
We recommend using mineral turpentine or AGM – Citrus Screenwash to help break down plastisol inks.
Alternatively, a m ore environmentally friendly option 1s to use the Fran mar Plastisol Ink Rem over.